It's Only A Number
Strategies to Reduce Lubricant Costs
As published in Production Machining
A person’s age is often said to be only a number, with overall health and fitness being the significant measures.
Cutting fluids, like all industrial lubricants, should be held to the same standards—it really is condition that matters.
By focusing on that philosophy, a shop can achieve immediate, sustainable cost savings.
Twice a week, on average, we get an urgent call from a lube manager, plant manager or someone else with
maintenance or operations responsibility. A mandate has been issued by higher-ups to reduce costs,
typically by 3 to 5 percent or more.
By the time we receive these calls, the mandate generally has some moss on it. The caller has been sitting on the
directive, weighing his options and postponing the dreaded paperwork. The “deadline” for his response is looming,
and he needs a strategy.
Fortunately, that’s the easy part. Outlining and thoroughly documenting how to achieve a 3-, 5- or even 7-percent
savings is relatively straightforward – particularly if the company, like 90 percent of industrial lubricant users,
changes fluids according to the clock instead of the condition. It’s even easier if the user is regularly adding fluids
to compensate for leakage.
A New Perspective
Sound lubricant management starts by changing how we think about the lubricants themselves.
For many companies, lubes are a commodity: Buy at the lowest cost, discard after a specific number
of hours of service, replenish as needed to make up for spills and leaks. A better approach, is to treat
them as assets, with attention to how they’re stored, dispensed, monitored and replaced. Overall costs will decrease –
often substantially so, and virtually always enough to meet that mandate. Here are three areas that
deserve particular attention.
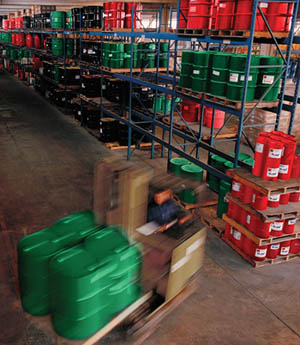
Proper lubricant storage is clean, dry and organized.
Storage: Lubricants degrade when storage practices are an afterthought. The most common storage problems
are damaged or improper containers, condensation, dirty dispensers, exposure to dust or fumes, poor outdoor
procedures, mixing of different products, exposure to extreme temperatures, and going beyond recommended
shelf life by failing to follow a FIFO (first in, first out) usage policy.
Handling: When it comes to lubricant handling practices, one of the most grievous issues comes from the use
of improper containers for lube top-offs. These containers allow water and other contaminants to enter,
shortening the life of the fluids.
Monitoring: If it’s an asset, it’s worth tracking. Lubes belong in tanks, not in absorbent socks, and shops need to
know how much oil is making its way to the latter and how much make-up is needed as a result.
When consumption is quantified, the results are always surprising. It’s not uncommon for “small” leaks throughout
large manufacturing facilities to total as much as 15 barrels of costly lubricant every month. While this is never good,
with the current high price of oil, many plants could buy a new tank or forklift with 1 year’s savings in lubricant,
absorbent and associated disposal costs. Proper monitoring is an easy way to reduce costs while sacrificing nothing.
Monitoring provides a baseline to benchmark improvements. It offers an HFI (hydraulic fluids index)
and provides everyone – maintenance supervisors, company management, purchasing department and others –
with a number for planning and operating purposes. And for those pursuing ISO 14001, tracking of lubricant against
disposal is a certification requirement.

Signum Oil Analysis from Acculube monitors critical indicators in used oil based on
leading equipment builder specs and international standards. The analysis allows lube managers
to monitor the condition of used oil and schedule replenishments or change-outs based on science,
rather than calendar notations.
The Heart of The Matter
After implementing good storage and handling procedures and identifying baseline numbers, serious changes
can be made. The most effective way to add life to oils is to let science, rather than a calendar, determine when they
should be changed. Standard tests including BN (base number), AN (acid number), RPVOT (rotating pressure
vessel oxidation test), and others (such as those that measure particulate contamination, corrosion performance
or viscosity) all help flag the point where fluids begin to degrade. These tests can also be used to predict this
critical juncture, making them valuable planning tools as well. Any oil use point can be sampled and monitored
in order to base change-outs on oil condition rather than time in service.
For a majority of machines and applications, the cost of even the most comprehensive testing is significantly
less than the labor and recharge costs – and loss of production time – of replacing fluids prematurely. For
companies that have implemented company-wide “green” initiatives or environmental policies to minimize waste,
extending fluid service life, stopping automatic discarding of fluids that still have useful service life and reducing
the volume of lube-soaked socks will go a long way toward the goal.
A related issue is the desire of many companies to reduce the use (and disposal) of zinc-containing products.
The HFI referenced earlier, and the strategies that can be implemented as a result, can produce substantial
cost savings and offer better performing alternatives to products containing zinc and other heavy metals.
Next time you’re feeling older than your years, let that feeling serve as a reminder to consider the condition of
your fluids. Are you getting as much life out of them as you could? If not, take action and put measures in place
to trim costs.
Acculube has extensive information on lubricant use, selection, safety, storage, dispensing and disposal,
and can recommend time and cost-saving lubricant strategies for you facility based on more than a quarter
century of experience with the region’s largest and most diverse users of industrial lubricant.
Story #1: Synthetic Lubricants or Conventional Oils: Making the Best Choice
Story #2: "Store Lubricant Oils and Greases Properly to Avoid Contamination, Deterioration, Poor Lubricant Performance – and to Save Time and Money."
Story #3: "Castrol Recognizes Provider of Value-Added Products and Services" (Acrobat file)
Story #4: It's Only a Number – Strategies to Reduce Lubricant Costs
Story #5: There Are 4 Main Reasons That Lubes Fail
Story #6: Cheap Hydraulic Oil
Back to Top
|